The critical reason for a wire and cable manufacturer to use a water blocking treatment in their product is to prevent access and dissipation of water and moisture throughout the cable. When deciding on which treatment to use (i.e. gel, yarn, or powder based) in your cable, it’s important to consider the advantages and disadvantages of each application method.
Posts by Eric Shippee
- By Eric Shippee
- 04/03/18
- 0 Comments
- By Eric Shippee
- 02/28/18
- 2 Comments
Tenacity and modulus are important characteristics to understand as they relate to industrial thread and yarn – particularly for applications in the wire and cable industry. They differ from one another in that tenacity is the ratio of tensile strength to yarn size. Tenacity is calculated using the ultimate breaking force of the yarn (when a thread or yarn is stretched to its breaking point) and the linear density and can be used to compare dissimilar material or different sizes of material.
Read more- By Eric Shippee
- 02/09/18
- 0 Comments
A creel is simply a frame on which the feeding thread or yarn bobbin is fitted. Often, the creel is fitted with a yarn tensioning device which controls tension variation. Proper placement and stabilization of thread and yarn at the beginning of the product manufacturing process is critical. “Think of a creel as the foundation of a building,” states Neal Fournier, Facilities & Maintenance Manager with Service Thread. “It’s likely that process improvement starts after the yarn enters the production process; however, you will be surprised by the gains that can be made by taking a look at using a creel or refining your creel design.”
Read more- By Eric Shippee
- 01/26/18
- 0 Comments
The practice of joining industrial yarn ends (resulting from breaks, defects, or end of the supply), is a critical component to the product manufacturing process, particularly in industries such as wire and cable (integration of ripcords), hose reinforcement, belting and more. When using industrial yarn in the production process, it is essential that the joining method endures the process without interruption and does not have a negative effect on the quality of the end product.
Read more- By Eric Shippee
- 01/19/18
- 0 Comments
Industrial yarn is designed and engineered to be incorporated into products where oftentimes, a functional requirement supersedes aesthetic considerations. Used by non-apparel industry product manufacturers, industrial yarns are typically a component part of a product to enhance the strength, durability, performance and other high-value properties of the product.
- By Eric Shippee
- 12/22/17
- 0 Comments
- By Eric Shippee
- 12/15/17
- 0 Comments
Polyethylene is the most commonly used plastic in the world, but how do you know if it’s the right yarn for your application? Consider the attributes of ultra-high-molecular-weight polyethylene (UHMWPE) - a very tough subset of polyethylene that has a strength to weight ratio 8-15 times greater than steel.
Read moreEric Shippee
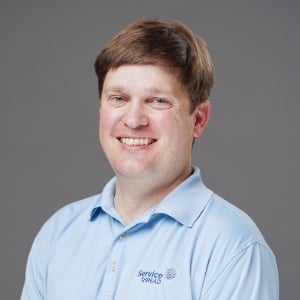
Recent Posts
Advantages And Disadvantages Of Various Water Blocking Treatments
- By Eric Shippee
- 04/03/18
- 0 Comments
The critical reason for a wire and cable manufacturer to use a water blocking treatment in their product is to prevent access and dissipation of water and moisture throughout the cable. When deciding on which treatment to use (i.e. gel, yarn, or powder based) in your cable, it’s important to consider the advantages and disadvantages of each application method.
Standard Tenacity Yarn vs. High Modulus Aramid Yarn – Which Do You Need?
- By Eric Shippee
- 02/28/18
- 2 Comments
Tenacity and modulus are important characteristics to understand as they relate to industrial thread and yarn – particularly for applications in the wire and cable industry. They differ from one another in that tenacity is the ratio of tensile strength to yarn size. Tenacity is calculated using the ultimate breaking force of the yarn (when a thread or yarn is stretched to its breaking point) and the linear density and can be used to compare dissimilar material or different sizes of material.
Read moreA creel is simply a frame on which the feeding thread or yarn bobbin is fitted. Often, the creel is fitted with a yarn tensioning device which controls tension variation. Proper placement and stabilization of thread and yarn at the beginning of the product manufacturing process is critical. “Think of a creel as the foundation of a building,” states Neal Fournier, Facilities & Maintenance Manager with Service Thread. “It’s likely that process improvement starts after the yarn enters the production process; however, you will be surprised by the gains that can be made by taking a look at using a creel or refining your creel design.”
Read moreThe practice of joining industrial yarn ends (resulting from breaks, defects, or end of the supply), is a critical component to the product manufacturing process, particularly in industries such as wire and cable (integration of ripcords), hose reinforcement, belting and more. When using industrial yarn in the production process, it is essential that the joining method endures the process without interruption and does not have a negative effect on the quality of the end product.
Read moreIndustrial yarn is designed and engineered to be incorporated into products where oftentimes, a functional requirement supersedes aesthetic considerations. Used by non-apparel industry product manufacturers, industrial yarns are typically a component part of a product to enhance the strength, durability, performance and other high-value properties of the product.
Polyethylene is the most commonly used plastic in the world, but how do you know if it’s the right yarn for your application? Consider the attributes of ultra-high-molecular-weight polyethylene (UHMWPE) - a very tough subset of polyethylene that has a strength to weight ratio 8-15 times greater than steel.
Read more