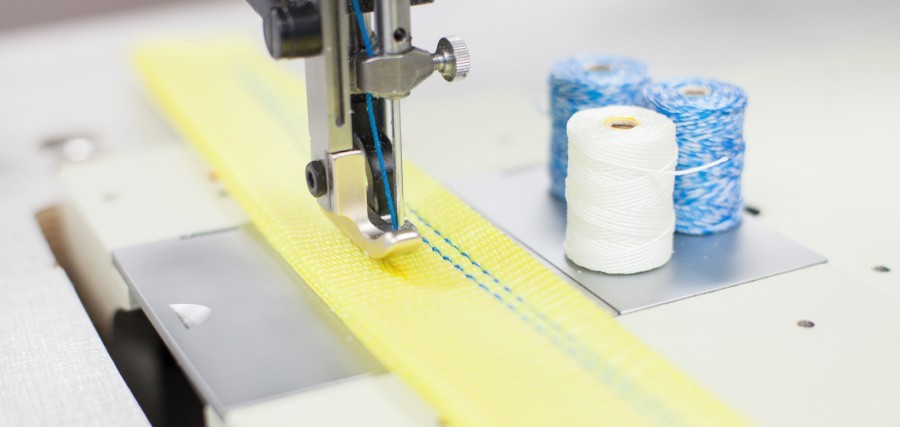
Singer Class 7 and other Class 7 sewing machines will run reliably for years if setup properly, oiled daily, and serviced regularly. These lock stitch machines were originally designed in the early 1900’s to use a bottom thread wound onto a flanged metal bobbin. This under bobbin thread, if not properly wound, will:
- Disrupt the timing of the machine
- Break needles creating a safety hazard to the operator
- Create downtime from clearing tangled thread and rework
- Require expensive machine repairs
To avoid these issues and increase efficiency, modern, high volume sewing operations use Style 41 (S41) pre-wound bobbins. These flange-less bobbins are engineered by thread manufacturers under controlled conditions and have advantages:
- Under bobbin tension control – pre-wound S41 bobbins are chemically treated to have uniform tension from start to finish. Metal operator bobbins vary.
- Uniform/Increased yardage per under bobbin – operator wound bobbins vary in length and are typically 20 to 30 yards per bobbin vs. 40 yards per pre-wound bobbin.
- Uniform Stitches – tighter stitches, less skipped stitches.
- Increased operator efficiency – more sewing, less prep work winding bobbins.
To convert a Class 7 machine to use pre-wound bobbins be sure to install a bobbin pin in the bobbin case. This part is avaiable from Service Thread or your local sewing machine repair shop. You can find detailed instructions on how to complete the five minute one time set-up here.
For more information or help with Class 7 parts, repairs, or supplies, click here.