What Causes Yarn to Break During Processing?
Periodic yarn breaks during processing can be a costly experience, particularly if you’re not sure why they’re happening. Here are a couple of things to check first:
- Contact points. Make sure there are no cracked guides, no burrs or cuts on any contact surface, and all rollers are turning properly.
- Check tension. Make sure your tensioner is set for the appropriate amount of tension and is functioning properly.
After you’ve made sure your tensioners are operating properly and have ruled out the possibility of different contact points causing damage to your yarn, the next thing to look at is the yarn package itself.
If you are still experiencing processing issues, particularly with slicker materials such as filament yarns and threads, your material may be sloughing. Sloughing occurs when one or multiple layers of yarn become loose on the supply package.
These loose layers can cause yarn to become trapped underneath or behind your yarn package as it’s running, resulting in tension spikes and yarn breaks.
One simple way to fix the issue is by using foam pads.
How do Foam Pads Protect Your Yarn?
Foam pads help to prevent yarn breakage because they prevent the yarn from falling underneath or behind yarn packages. This is especially important during high-speed processing, when yarn falling into gaps under the packages would cause constant snags and breaks.
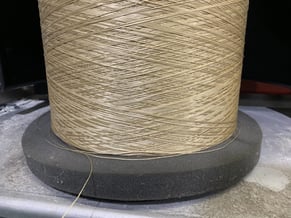
Foam pads also provide a cushioned but firm base where the yarn can rest. The pads help dampen the impact created by the processing equipment, absorbing some of the energy that comes from centrifugal forces and any jarring or bouncing that could potentially occur
What Types of Applications Can Benefit From Using Foam Pads?
Equipment that can benefit from using foam pads includes:
- Sewing machines
- Braiders
- Spiral winders, knitters, and decks
- Creels
If you are running spiral decks and winders at very high speeds, keeping them constantly in motion, foam pads may need to be replaced at every shift. At lower speeds, your foam pads may last longer. If the equipment only runs periodically, foam pads will last even longer.
How often should foam pads be replaced? The simple answer is: whenever they no longer provide the same level of function as initially intended. The key is to make sure that the foam pads always make full contact with the base of the yarn package.
What Thickness Do I Need?
Foam pads are typically at least ¾-inch thick. You may need a thicker foam pad if you are using extremely high-speed equipment, which will wear them down faster, or if you’re using very heavy yarn that adds to the energy load handled by the pad. You also may need thicker pads if the amount of cone or tube exposed still leaves a gap underneath the yarn package.
Incorrectly Sized Pad Correctly Sized Pad
For heavy industrial uses, some pads are 2 or more inches thick. Check with your foam pad supplier to see exactly which thickness you should order for your exact specifications.
Where Can I Find Out More About Ways to Improve How My Yarn Processes?
Service Thread processes a wide variety of industrial textile fibers and provides processing support for industrial manufacturers. We are dedicated to supporting our customers with technical expertise and education.
Our on-staff experts can advise you about best practices for industrial yarn processing, so your operation stays as productive as possible. Contact Service Thread today for more information.