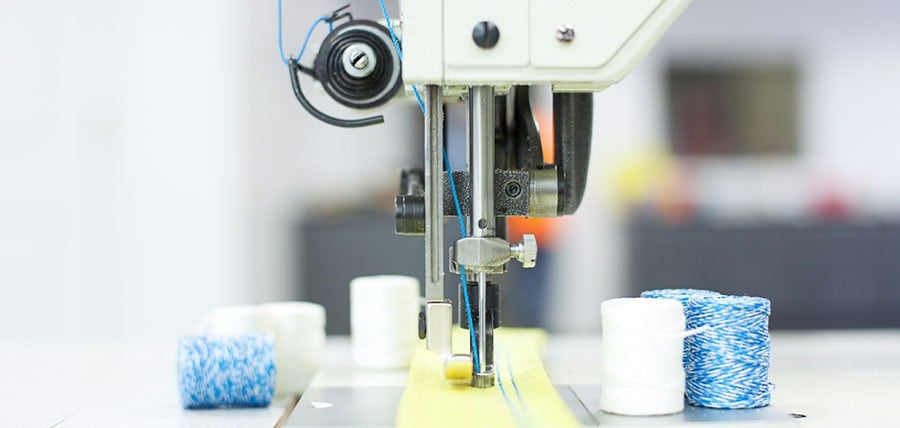
How many reasons can you think of to apply lubrication to thread?
I’ve found four fantastic ones:
1. To Act as a Heat Sink Between Needle and Thread. Needle temperatures as high as 350 degrees C (662 degrees F) have been recorded during sewing! A good lubricant will protect thread from these extreme temperatures, preventing it from melting and breaking, by dissipating the heat.
2. To Act as a Heat Sink Between Needle and Sewn Material. Lubricants should be capable of transferring from the thread to the needle, reducing the needle’s friction with the sewn material and thus its temperature.
3. To Reduce Friction. Apply lubrication consistently, minimizing variation in the short- and long-term. Uniform, easily controlled sewing tensions are critical for achieving sewing performance and quality. What happens when you apply lubrication inconsistently? The thread will chatter through the tension discs, causing areas of “stick-slip.” You wind up with a bad break or skipped stitches, or both.
4. To Prevent Filament-to-Filament Damage. As a thread passes through a sewing machine, it is subjected to repeated cycles of flexing and abrasion, and then a final impact from the needle eye as it enters the material.
Do you have any questions about thread lubricant that I can help answer? Ask away!