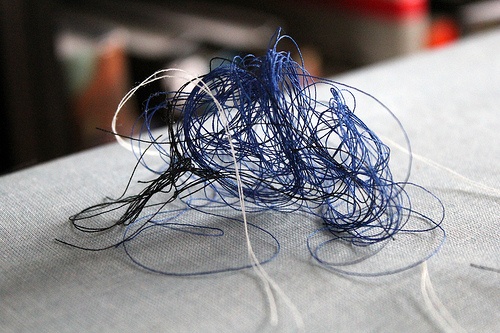
As discussed earlier, there is nothing worse than trying to handle a torque/tension filled lively, kinky yarn or thread. Each step of a manufacturing process such as twisting, spinning etc. causes tension in fiber, filament, yarn and thread. Yarns tend to snarl/kink up in order to relax and rid themselves of tension. Uncontrolled tension and subsequent snarling & kinking are likely to create manufacturing issues for our customers, and we do not want that!
The Solution
Thermally Condition or Heat-set stressed out fibers and/or filaments by imparting dimensional stability through their exposure to a wet or dry heat source.
H&W Yarn Conditioner
Our preferred method for stabilizing polyester and nylon yarn is the H&W Conditioning oven which is known for its ability to impart a temporary memory and in most cases will have little effect on yarn physical properties. There are many conditioning cycles that can be used which utilize various combinations of Wet and Dry Heat, and time, and in most cases a 15 - 20 minute Pre-Heat will be used at the start of a cycle. Generally speaking, a very high Twist Balance (> 20) may require high Wet and Dry bulb settings, 200 - 210°F, and a total cycle time of up to 8 hours. A TB of 5 - 20 may only require Wet and Dry bulb settings of 180 - 190°F for 2 - 4 hours. Materials such as polypropylene may require Wet and Dry bulb temperatures as low as 160 - 170°F and a cycle time of 3 – 5 hours. For yarns with a high twist and therefore TB >20, I prefer to have a Wet bulb time that is at least 50% of the total cycle time.
Autoclave
A device which is commonly used for stabilizing and even curing materials is an autoclave. The current autoclave design was invented in the 1880s by Charles Chamberland and allows for the treatment with steam under vacuum, subjecting materials to high pressure saturated steam and thus, in some cases working temperatures as high as 140°C. (At atmospheric pressure water will boil at 100°C, but when the pressure is 15 psi (1 atmosphere) above standard pressure (760 mm Hg), water boils at 121°C. Increasing the pressure increases the temperature). Autoclaving will generally impart a permanent memory into yarn and will change many of its physical characteristics e.g. denier, elongation at break, shrinkage.
Download our guide below for helpful tips on best practices and the latest processing tools available to help control yarn tension and other variables that can affect the application of binders, ripcord and strength member into your manufacturing process.